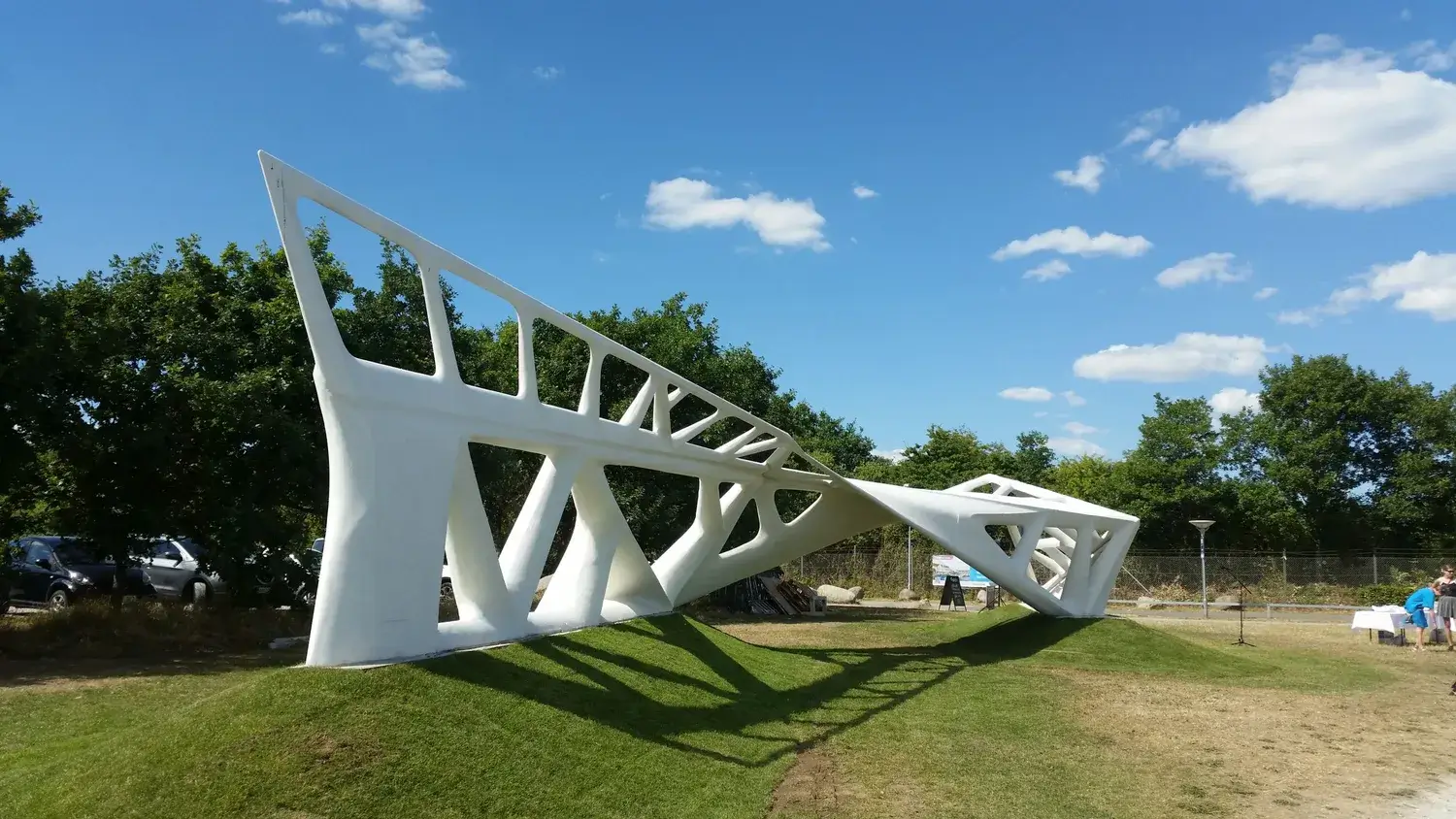
EXPLORE OUR PUBLICATIONS
Welcome to Hi-Con's Knowledge Center, your ultimate resource for information about our innovative solutions and products in Ultra High Performance Concrete (UHPC). As a leading producer of UHPC since 2001, we specialize in creating stylish and customized balconies, stairs, facades, and bridges using our concrete type, CRC.
Our Knowledge Center is dedicated to providing valuable insights, test results, documentation, calculations, and product declarations. Whether you are a current customer or simply curious about concrete, we invite you to explore our materials and discover the endless possibilities.
We hope you enjoy delving into our universe and becoming more familiar with our material. If you have any questions or suggestions for topics you'd like us to cover, please feel free to contact us.
We are always eager to hear from you and help you learn more about our innovative concrete solutions.
Unsure about what UHPC CRC i2 actually is? We suggest you read more about it here: