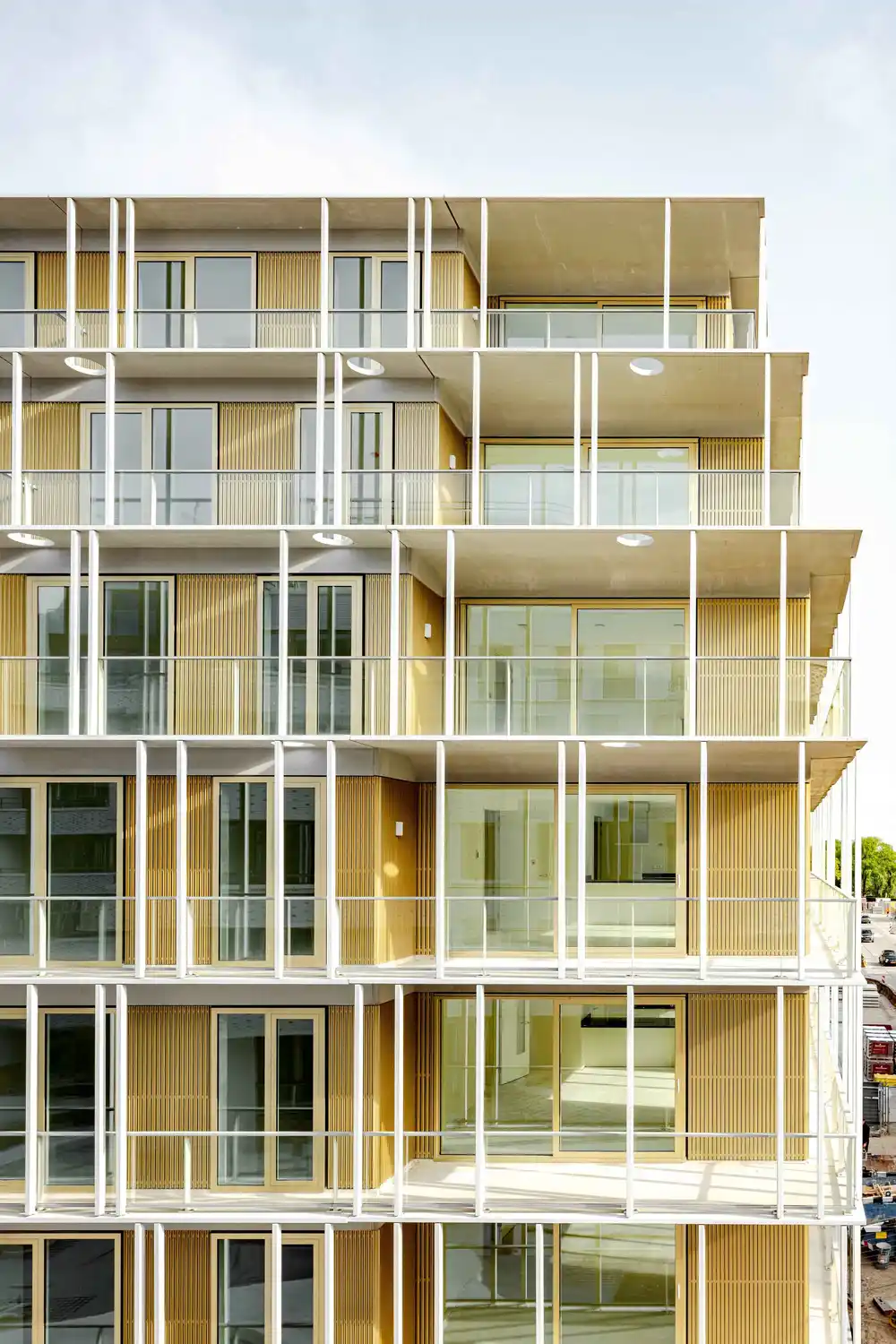
11. July 2025
A mock-up balcony on an old building is installed using a glued connection: Ved Volden in Copenhagen, Denmark.
In many of the previous blog posts, we have shown various ways to use Ultra High Performance Concrete, but most examples have been new construction projects.
In a series of three blog posts - this being the first, we will illustrate some of the benefits, but also some of the challenges of using Ultra High Performance Concrete (UHPC) in renovation projects.
The first post in this mini-series will address glued connections in balcony renovations, but first, we will start with a brief and general introduction to renovation.
When considering renovating, extending, or adding balconies to an existing structure, the reserve for unused structural capacity is crucial, and in this regard, the building type is important.
Newer buildings made of concrete or steel will often have some surplus capacity and are rarely subject to protection, which leaves more options for attaching balconies.
However, older brick buildings (from the 1930s and 40s or even older) have the general challenge that the walls cannot support too much load - both vertically and especially horizontally. This means that if external columns cannot be used, only the deck is available for attaching balconies to the building.
If the deck is made of concrete, existing balconies will have been made by in-situ casting an extension of the deck that goes out to the balcony slab. This is the building type I will focus on in this blog post.
In principle, most connections are glued to some extent: Most brackets are attached using 'chemical anchors,' so when using only threaded rods and adhesive without brackets, it is essentially just applying many chemical anchors as the sole means of fixation.
So, with all the above challenges - why use glued connections in Ultra High Performance Concrete?
First and foremost, because in relevant cases, there is no real alternative.
When a concrete element is needed - for aesthetic or other reasons - there are significant challenges associated with replicating the old structure in regular concrete because standards and norms have changed drastically since the building was designed.
Requirements for cover layers, fire resistance, and most importantly, the live loads that the balcony must support have all increased significantly. The live load alone is challenging enough. Therefore, it is not possible to cast a new copy of the original balcony - it would not meet today's requirements - but with Ultra High Performance Concrete, it is possible to create elements with much lower weight than the original, compensating for the increased live loads.
In summary, the combination of glued connections and lightweight balconies in Ultra High Performance Concrete can be the difference that makes renovation possible in some extreme cases - but this is certainly not without challenges.
As far as renovation principles go, bonded connections are by far the most complex and require a lot of planning, documentation, and pre-approvals, risk management, and creative thinking and on-the-fly problem-solving in both the design and construction phases.
So, this is exactly how we like it at Hi-Con: Challenging and complex, and therefore very rewarding when we succeed together with our partners!
Interested in learning more about Ultra High Performance Concrete?
FILL OUT THE FORM AND WE'LL GIVE YOU A CALL