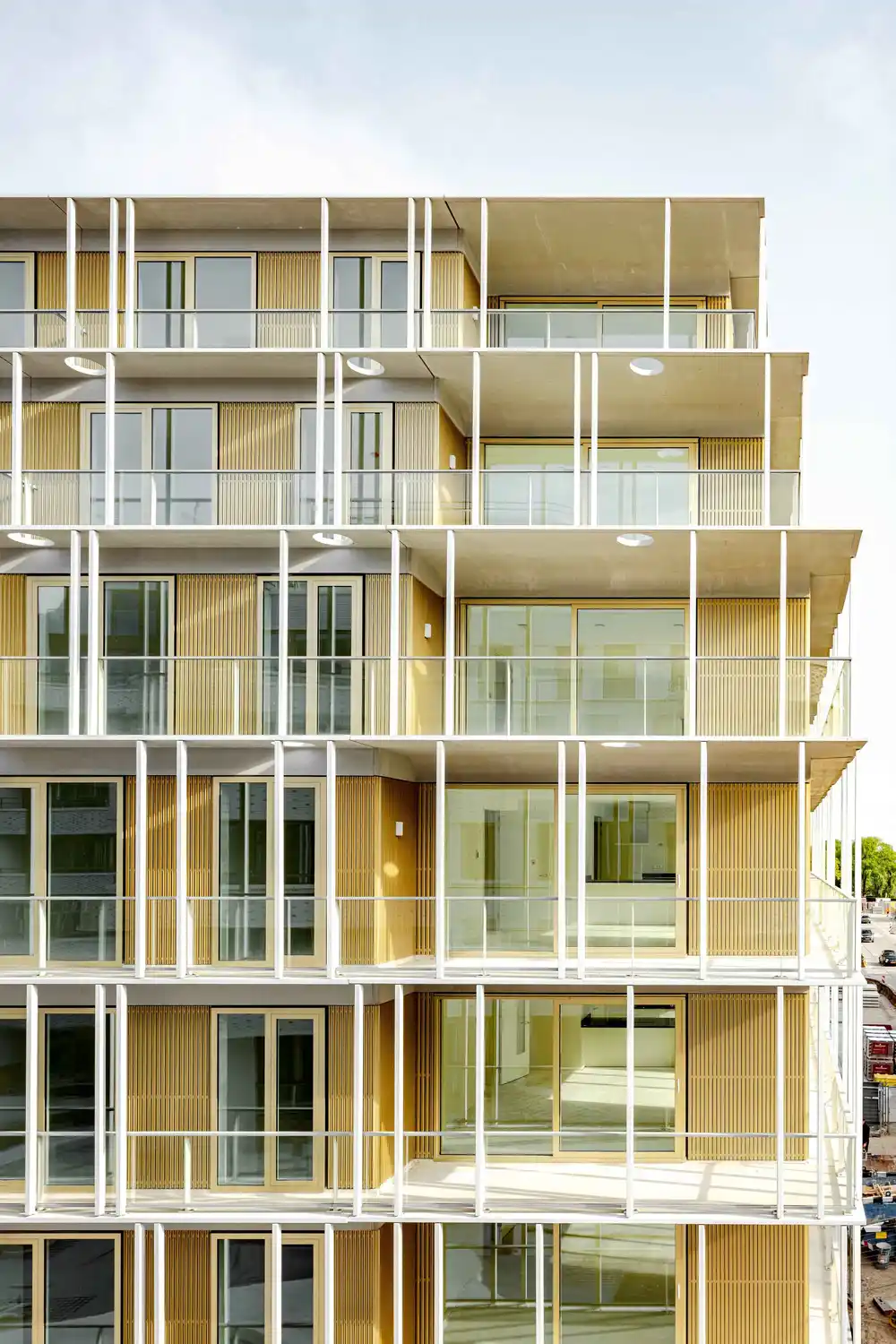
11. July 2025
In one of our previous posts "CRC Application Cases - Sustainability," we commented on how difficult it is to compare the environmental footprint of Ultra High Performance Concrete CRC with other materials - and used this as an excuse for why we have not yet put together an EPD (Environmental Product Declaration) for our products. To be honest, it was not something we rushed to do, as we knew that the high cement content and steel fibers in CRC would likely not give us the best result - and although EPD and LCA (Life Cycle Analysis) have been discussed for years, it has rarely been a requirement for projects.
However, we quickly realized that if we are not part of paving the way for this, it would be difficult to be world leaders in UHPC, and therefore we have now developed an EPD for Hi-Con balconies.
We based our EPD on two representative projects - and chose them to cover our range of balconies as well as possible in terms of how many m2 we get per m3 CRC, how many molds are needed, and how large the brackets had to be for installation, etc.
We are ready to help you with your project.
FILL OUT THE FORM AND WE WILL CONTACT YOU